Before starting to wind the cable, you first need to understand the basic characteristics of the cable, such as the cable's material, specifications, endurance, etc. This information is essential for selecting the appropriate reel, setting winding parameters and taking appropriate protective measures.
2. Choose the appropriate reel
Before choosing a reel, you first need to clarify the specifications of the cable, including the diameter, length, weight and material of the cable. This information will directly affect the size, load-bearing capacity and material selection of the drum. The diameter of the drum should be determined based on the diameter of the cable and the required bending radius. Generally, the winding radius of the cable on the drum should be greater than the minimum bending radius of the cable to prevent the cable from being damaged by excessive bending during the winding process. The length of the drum should be sufficient to accommodate the length of the cable and leave a certain amount of space to facilitate the winding and fixing of the cable. The drum needs to be able to withstand the weight of the cable as well as the shock and vibration that may occur during transportation and use. Therefore, when selecting a drum, you need to evaluate whether its load-bearing capacity meets your needs. Usually, the load-bearing capacity of a drum is clearly stated in its technical specifications. The material of the drum should have good wear resistance, corrosion resistance and load-bearing capacity. Common reel materials include steel, stainless steel, aluminum alloy and plastic. Rolls made of different materials have different characteristics and applicable scenarios, and they need to be selected according to the actual situation.
3. Set reasonable winding parameters
When winding cables, reasonable winding parameters need to be set, including winding speed, winding tension, etc. Wrapping too fast or using too much tension can cause damage to the cable. Therefore, when setting winding parameters, the material and specifications of the cable should be fully considered to ensure that the cable can maintain appropriate tension and speed during the winding process.
4. Take protective measures
To ensure that the cable is not damaged during the winding process, a series of protective measures need to be taken. First of all, before winding the cable, the surface of the cable should be checked for damage or defects. If found, it should be dealt with in time. Secondly, during the winding process, friction or collision between the cable and the drum or other objects should be avoided to reduce the risk of cable damage. In addition, a layer of protective agent can be applied to the surface of the cable to improve the cable's wear resistance and corrosion resistance.
5. Follow the correct winding method
Proper wrapping method is critical to protecting cables. When winding cables, follow the spiral direction of the cables and keep the cables neatly arranged. If the drum is equipped with a winding guide device, it should be wound according to the requirements of the guide device. In addition, avoid moving the cable at sharp angles during the winding process to prevent cutting the cable. At the same time, it is also necessary to pay attention to the tension changes of the cable during the winding process, and adjust the tension in time to keep the cable flat and stable.
6. Regular inspection and maintenance
To ensure that the cable is wound on the drum in good condition, regular inspection and maintenance is required. Regular inspections should include surface inspection of cables, inspection of winding parameters, and inspection of reels. If the cable is found to be damaged or the winding parameters are inappropriate, it should be processed and adjusted in time. In addition, the drum and cable surfaces need to be cleaned regularly to maintain a good working environment.
7. Use appropriate tools and auxiliary equipment
In the process of winding cables, some suitable tools and auxiliary equipment can be used to improve the winding quality and efficiency. For example, you can use a cable reel to quickly and neatly roll up cables to avoid the problem of tangled cables. In addition, methods such as binding and casing can be used to fix and protect the cable to prevent it from being damaged during the winding process.
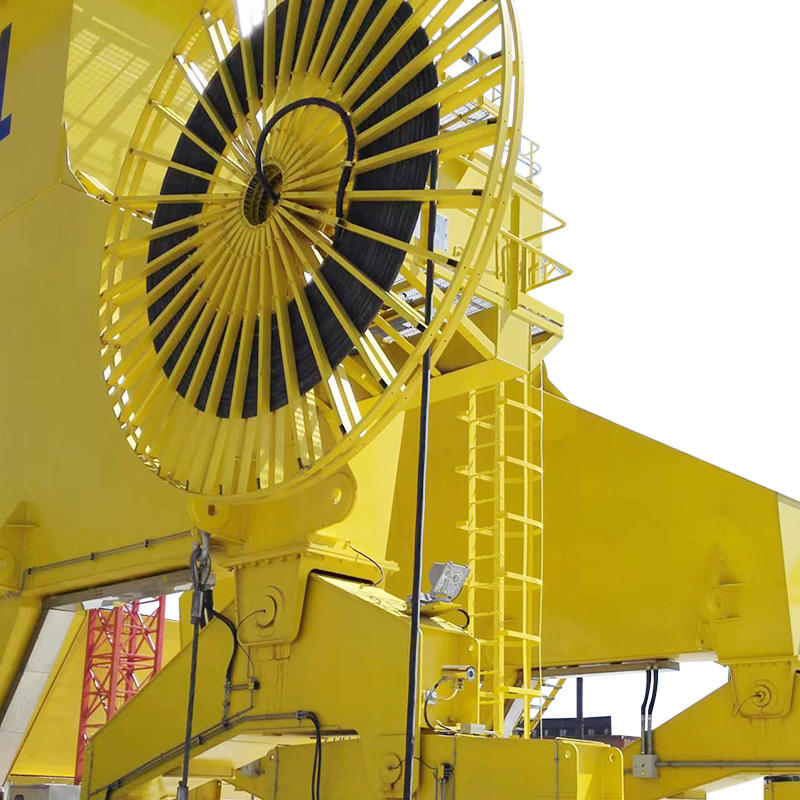